For previous article, please refer to Solutions to plastic product mold opening problems (1).
This article mainly introduces problems that arise during mold opening, mold trial and mass production processes after design of plastic parts is completed. It also provides a general understanding of how to solve them. Details are as follows;
Mainly following points;
1. Silver streaks, bubbles and pores
2. Weld marks
3. Brittle
4. Discoloration
5. Dark brown spots
1. Silver streaks, bubbles and pores
Material is disturbed by gas during mold filling process, and silver streaks or tiny bubbles often appear on the surface of product, or bubbles are formed in thick wall of product. Main source of these gases is that raw materials contain moisture or volatile substances or excessive lubricants. It may also be that material temperature is too high and plastics are heated for a long time, causing degradation and generating degradation gases. There are many reasons for this, factors involved may include injection molding machines and molds.
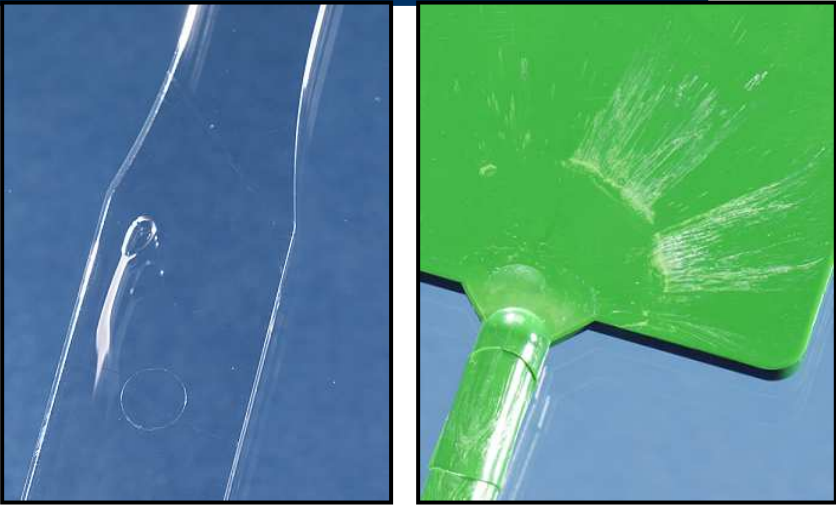
(1) Injection molding machine
① Nozzle part may be clogged. Nozzle hole of injection molding machine is too small, material is cast or drawn at nozzle, there are obstacles or burrs in barrel or nozzle, and frictional heat is generated when high-speed material flow passes by, causing material to decompose.
② Whether temperature controller of injection molding machine is accurate and whether there is any difference in control.
(2) Mold
① Check whether gate and flow channel are blocked. If necessary, increase gate depth and flow channel diameter. Due to design defects, such as poor gate position, too small gate, asymmetric gate arrangement of multi-gate parts, small flow channels, unreasonable mold cooling system, large mold temperature difference, etc., melt flow in mold cavity is discontinuous, blocking air channel.
② Check that exhaust condition is good and deepen or increase exhaust if necessary. Mold parting surface lacks necessary exhaust holes or exhaust holes are insufficient, blocked, or poorly positioned, there are no processing gaps such as inserts and ejector pins for exhaust, resulting in air in cavity not being able to leave at the same time as plastic enters. .
③ Surface roughness of mold is poor and friction resistance is large, causing local hot spots and decomposing passing plastic.
④ Mold surface temperature is too low, increase mold temperature.
⑤ If there is too much release agent on mold surface, limit use of release agent or switch to silicone-free release agent.
⑥ Check for oil leakage during molding. Water leakage will contaminate mold cavity.
(3) Injection molding process
① Melt temperature is too high and there are too many volatiles, so lower barrel temperature. If barrel temperature is too high or heating is out of control, barrel temperature should be reduced step by step. Temperature of feeding section is too high, causing part of plastic to melt prematurely and fill screw channel, and air cannot be discharged from feeding port.
② Injection pressure is small and pressure holding time is short, so that molten material does not adhere closely to the surface of cavity.
③ If injection speed is too fast, molten plastic will be decomposed by large shear, producing decomposition gas; if injection speed is too slow, mold cavity cannot be filled in time, resulting in insufficient surface density of product, resulting in silver streaks. Increase or decrease speed of ejected colloid.
④ Melt temperature is too low so that filling is unstable, internal stress increases, material temperature and nozzle temperature increase accordingly. Insufficient material quantity, too large feeding cushion, too low material temperature or too low mold temperature will affect flow of the melt and molding pressure, resulting in bubbles.
⑤ Use multi-stage injection to reduce silver streaks: medium-speed injection to fill runner → slow speed to fill gate → fast injection → low-pressure and slow speed to fill mold so that gas in mold can be eliminated in time in each section.
⑥ Rubber material remains in barrel for too long, and the total cycle time needs to be reduced.
(4) Raw materials
① If raw materials are mixed with different types of plastics or pellets are mixed with a large amount of powder, air will easily be entrained during melting, and sometimes silver streaks will appear. When raw materials are contaminated or contain harmful debris, they are prone to thermal decomposition.
② Structure of recycled material particles is loose, and amount of air stored in micropores is large; recycled material has been regenerated too many times or ratio to new material is too high (generally should be less than 20%).
③ Raw materials contain volatile solvents or liquid additives in raw materials (such as dyeing auxiliary white oil, lubricant silicone oil, plasticizer dibutyl ester, stabilizers, antistatic agents, etc.) are too much or unevenly mixed, and enter mold cavity in an accumulated state, forming silver streaks.
④ Ensure that raw materials are fully dry and remove moisture. Plastic is not dried or absorbs moisture from atmosphere. Raw materials should be fully dried and a drying hopper should be used.
⑤Some brands of plastic cannot withstand higher temperatures or longer heating times. Especially when containing trace amounts of moisture, catalytic cracking reactions may occur. For this type of plastic, it is necessary to consider adding external lubricants such as stearic acid and its salts (up to 50g per 10kg of material) to reduce processing temperature as much as possible.
(5) Design
Wall thickness is too thick, cooling speeds inside and outside are different. During mold manufacturing, size of main channel, runner and gate should be appropriately increased.
2. Weld marks
Weld marks refer to lines where cold material melts on the surface of plastic parts. When molten plastic in cavity meets inserts, holes, areas with discontinuous flow rates, areas where filling material flow is interrupted and merges in multiple strands, and when gate injection mold filling occurs, linear welding marks are produced because they cannot be completely fused. Existence of weld marks greatly weakens mechanical strength of product. Method to overcome weld marks is basically same as method to reduce dent of product. There are many reasons for weld marks, and factors involved may include molds, processes, raw materials, product design, etc.
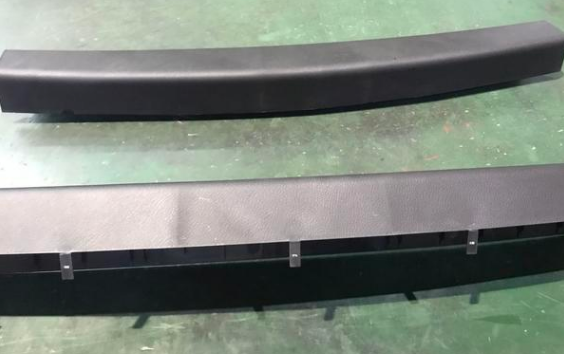
(1) Injection molding machine
Poor plasticization and uneven melt temperature can extend molding cycle, make plasticization more complete. If necessary, replace machine with a large plasticizing capacity.
(2) Mold
① If mold surface is too cold, mold temperature should be appropriately increased or local temperature at weld joint should be increased purposefully to limit coolant speed.
② Flow channel is small, too narrow or too shallow, and cold material well is small. Size of flow channel should be increased to improve efficiency of flow channel and at the same time increase volume of cold slug well.
③ Expand or reduce gate cross-section and change gate position. Gate and runner are too small, increase gate size and increase runner diameter; gate is too far away from welding area, it is necessary to change gate position or add an auxiliary gate; when opening gates, try to avoid melt flow around inserts and holes. Gate where injection molding occurs must be modified, relocated or buffered with blocks. Try to use less or less multiple gates.
④ If exhaust in mold is insufficient or there are no exhaust holes, exhaust channels should be opened, expanded or dredged, including using gaps between inserts and ejector pins to exhaust, adding exhaust holes in welding area or increasing size of exhaust holes.
⑤ If too much detergent is used, use no release agent as much as possible.
⑥ Plastic parts are too thin in welding area, and mold needs to be modified to thicken material.
(3) Injection molding process
① Effective cavity pressure is too low, increase injection pressure and extend injection time.
② Increase injection speed. High speed can allow molten material to reach confluence point before it has time to cool down. Low speed can allow air in the cavity to be discharged.
③ Increase melt temperature and temperature of nozzle. The higher temperature, the lower viscosity of plastic, the smoother flow pattern, and the thinner weld line; the lower temperature, the less decomposition of gaseous substances.
④ Release agents should be used as little as possible, especially silicon-containing release agents, otherwise material flow will not be fused.
⑤ Reduce mold clamping force to facilitate exhaust.
⑥ Appropriately increase back pressure and adjust screw speed to obtain a higher and more uniform melt temperature; increase screw speed to reduce plastic viscosity; increase back pressure to increase plastic density.
(4) Raw materials
① Ensure that raw materials are well dried. Ingredients should be dry and liquid additives in formula should be minimized.
② Improve its fluidity, appropriate lubricants and stabilizers to plastics with poor fluidity or high heat sensitivity, and switch to plastics with good fluidity or high heat resistance if necessary.
(5) Product design
① Wall thickness is small, and parts should be thickened to avoid premature solidification.
② Position of insert is improper and should be adjusted.
3. Crispy
Brittleness occurs when injection molded parts break when ejected or are easily broken after being ejected from mold. Brittleness is mostly caused by internal stress. There are many reasons for brittleness of products. Factors involved may include injection molding machines, molds, processes, raw materials, product design, etc.
(1) Injection molding machine
① Whether there are any dead corners or obstacles in barrel, which may easily promote degradation of melt and require thorough cleaning.
② Plasticizing capacity of machine is too small, and plastic is not fully plasticized in barrel; plasticizing capacity of machine is too large, plastic is heated and sheared in barrel for too long, and plastic ages easily, making product brittle. Therefore, plasticizing capacity should be increased.
③ If ejection device is tilted or unbalanced, ejection cross-sectional area is small or improperly distributed, adjust it according to specific situation.
(2) Mold
① If gate is too small, you should consider adjusting gate size or adding an auxiliary gate.
② If shunt is too small or improperly configured, try to make it balanced and reasonable or increase size of shunt.
③ Poor mold structure causes abnormal injection molding cycle, increases mold temperature, and limits coolant circulation speed.
(3) Injection molding process
① If melt temperature is too low and material is easily degraded, temperature of barrel (rear area) and nozzle should be increased.
② If melt temperature is too high, material will easily degrade. It is necessary to reduce barrel temperature in each area as well as screw pre-molding back pressure and speed.
③ If mold temperature is too high, it will be difficult to demould; if mold temperature is too low, plastic will cool down prematurely, weld seam will be poorly fused, and it will easily crack. Set appropriate mold temperature.
④ Increase injection speed to ensure fusion strength.
(4) Inspection
① If it is contaminated by heterogeneous glue (other raw materials with low melting points) or bad additives, dust and other impurities, identify cause and clean it thoroughly.
② Internal stress of injection molded parts is too large and has not been released, so it needs to be annealed.
③ Content of recycled materials is too high or recycling times are too many, and dosage needs to be controlled through experiments.
(5) Product design
① Product design has sharp corners, gaps or parts with widely different thicknesses that are prone to stress cracking.
② Product design is too thin or has too many hollows.
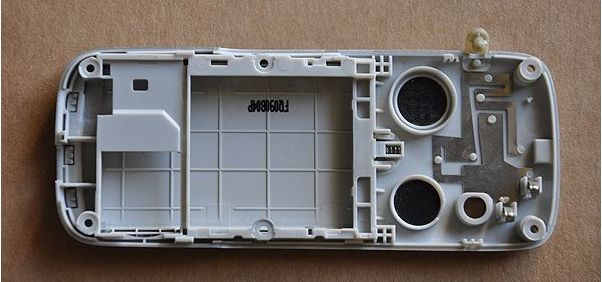
4. Discoloration
Discoloration means that color of surface of injection molded part is inconsistent with required color. There are many reasons for discoloration, including injection molding machines, molds, processes and raw materials.
(1) Injection molding machine
① Equipment is not clean and needs to be cleaned. Dust or other dust deposits on hopper will cause contamination and discoloration of materials.
② Thermocouple, temperature controller or heating system is out of tune causing temperature control failure.
③ There are obstacles in barrel, which can easily promote degradation of plastics; there are metal foreign objects stuck in barrel or screw groove, and continuous grinding will cause plastic to change color.
(2) Mold
① Mold is poorly vented, plastic is adiabatically compressed, reacts violently with oxygen under high temperature and high pressure, and burns plastic.
② Mold gate is too small.
③ There is too much lubricant and release agent in material or in mold. If necessary, barrel should be cleaned regularly to remove antistatic and other additives that are worse than heat resistance of plastic.
④ Size of nozzle hole, main channel and branch channel are too small.
(3) Injection molding process
① Screw speed is too high and pre-molding back pressure is too high.
② Temperature of barrel and nozzle is too high.
③ Injection pressure is too high, time is too long, and injection speed is too fast, causing product to change color.
(4) Raw materials
① Material is contaminated
② High moisture and volatile content.
③ Decomposition of colorants and additives
5. Dark brown spots
Black spots or black liquid refer to injection molded parts showing black spots or stripes, and there is no fundamental change in the color of injection molded parts. Warpage deformation may be caused by injection molding machine, mold, raw materials, etc.
(1) Injection molding machine
Rubber material has a “dead spot” in non-flowing area of barrel device, which causes it to remain at high temperature for too long and turn into charred material. Barrel and screw need to be disassembled, surfaces in contact with polymer need to be thoroughly cleaned.
(2) Mold
① Wall part of injection molded part is too narrow, and material decays when it flows under high pressure. It needs to be checked and corrected to maintain accuracy and consistency of wall thickness.
② Mold gate is too small, oil has penetrated from ejection device or there is oil in cavity, and gate size needs to be increased.
(3) Raw materials
① Raw materials are not clean, and multiple recycled rubber materials are mixed into materials. Check source and remove impurities.
② Lubricant is insufficient and an appropriate amount of lubricant needs to be added.
For further doubt, please refer to Solutions to mold opening problems for plastic products (3).
2 thoughts on “Solutions to plastic product mold opening problems (2)”