For previous article, please refer to Solutions to plastic product mold opening problems (2).
This article mainly introduces problems that arise during mold opening, mold trial and mass production processes after design of plastic parts is completed. It also provides a general understanding of how to solve them, as detailed below.
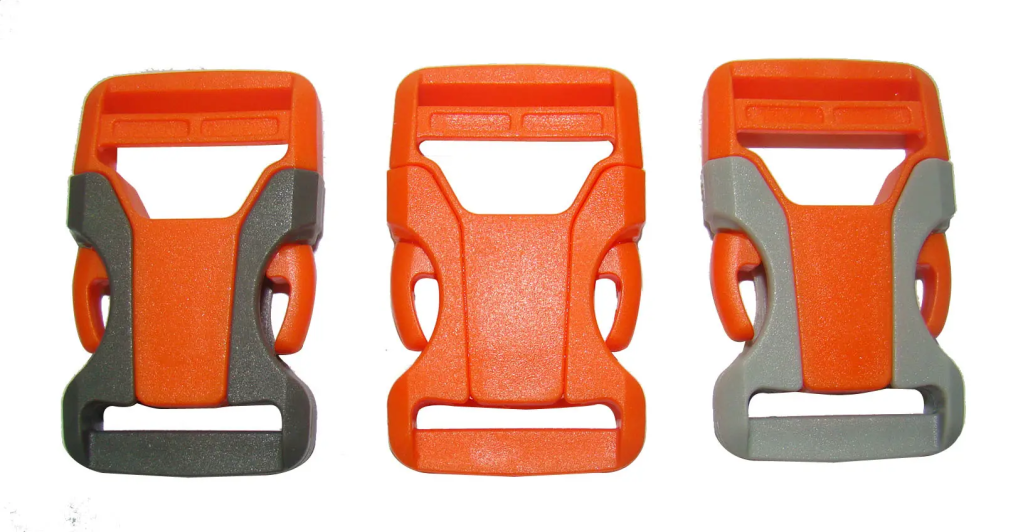
Mainly following points:
1. Rupture
2. Rough surface
3. Difficulty in demoulding
4. Warping deformation
5. Dimensional instability
1. Rupture
Cracking refers to small cracks or cracks on the surface of an injection molded part. Rupture may be caused by injection molding machine, mold, process, raw materials, etc.
(1) Injection molding machine
Main reason is that plasticizing capacity is insufficient, that is, plasticizing capacity is small and plasticizing is insufficient, and it needs to be replaced with a machine with a larger plasticizing capacity.
(2)Mold
① Poor exhaust can easily form water lines and reduce strength.
② If gate is too large, injection molded parts will be over-stressed and gate size will be reduced.
③ If there is water leakage in cavity or core, check whether there are fine cracks in mold.
④ Design of injection molded parts is too thin and requires adding reinforcement ribs.
⑤ Check whether mold cavity and core have sufficient demoulding angle.
⑥ Ejector oil is transmitted to the surface of mold cavity and mold is inspected.
⑦ Increase diameter of ejector pin and reduce ejection speed of ejector pin.
(3) Injection molding process
①Adjust barrel temperature. If temperature is too high, material will degrade; if temperature is too low, welding strength will be insufficient.
②Adjust injection pressure. Increase temperature to make mold filling smooth and reduce viscosity; too high pressure will cause internal stress to easily crack, so it needs to be reduced.
③ Reduce pre-molding back pressure and screw speed to avoid rubber degradation.
④ Increase injection speed appropriately.
⑤ Increase cooling time. If cooling time is too short and it is not fully hardened, it will easily crack or turn white when ejected.
(4) Raw materials
① Ensure that raw materials are fully dry.
② If raw materials are contaminated, find out cause and control it.
③ Add too much recycled material, and use test results to determine appropriate addition ratio.
2. Rough surface
Rough surface means that surface accuracy of injection molded part is not good, or accuracy is inconsistent everywhere, and some parts are glossier than others. Main causes of surface roughness may be injection molding machine, mold, process and raw materials.
(1) Injection molding machine
① Insufficient supply.
② Barrel is not cleaned when changing materials.
③ Check whether there is cold glue dripping from nozzle.
(2) Mold
① Gate is too small or runner is too thin. Increase gate or use a thin sheet to form a gate to let in water.
② Surface roughness of mold cavity is poor, needs to be polished, improved and checked for water leakage.
③ If exhaust is poor, add exhaust holes to parts with poor surface gloss to improve it.
④ Enlarge or increase cold material well to collect cold material.
⑤ Mold temperature is too low and mold temperature needs to be increased.
⑥ It may be due to influence of release agent. Stop using release agent.
(3) Injection molding process
① Increase melt temperature (check whether barrel heating belt is disordered, temperature is uneven, and temperature is too high or too low locally).
② Nozzle temperature needs to be increased.
③ It may be filled too fast or excessively sheared, so lower injection speed appropriately.
④ Increase injection pressure.
⑤ Extend injection time.
(4) Raw materials
① Raw materials are not dried.
② Too much recycled material is added, or recycled material degrades multiple times.
③ Excessive dosage of release agent.
3. Difficulty in demoulding
Difficulty in demoulding (gate or plastic part is compressed in mold) means that injection molded part (or together with the gate) is stuck or compressed in mold and cannot be ejected or is difficult to demould. Main reasons may be mold and process.
(1) Mold
① Design has unreasonable undercuts, demoulding structure is unreasonable or position is improper, and needs to be corrected.
② Draft angle in mold is not enough. Modify mold and increase angle.
③ Surface of mold is scratched and scratched. Sprue wall or surface of cavity is rough and needs to be polished.
④ Highly polished mold surface will make it difficult for injection molded parts to be ejected from mold under action of vacuum negative pressure.
⑤ Ejection mechanism is inappropriate and needs to be corrected.
(2) Injection molding process
① Injection volume is too much, mold is overfilled with rubber material, injection volume, injection pressure and injection speed are reduced.
② Material temperature is too high and needs to be lowered appropriately.
③ Pressure holding time is too long and screw forward time is reduced.
④ Increase cooling time or shorten cooling time (depending on mold cavity or core sticking).
⑤ Use release agent to release mold if permitted.
4. Warping deformation
Warpage deformation means that shape of injection molded part is similar to mold cavity, but it is warped or deformed. Warpage deformation may be caused by molds and processes.

(1) Mold
① Increase cooling capacity of mold, speed up coolant speed, and lower mold temperature to increase hardness of outer surface of plastic part.
② Whether gate position is at the thickest position.
③ Increase gate size and runner size, make runner as thick and short as possible, and reduce orientation of molding.
④ Check whether core and cavity are deflected, resulting in thin wall thickness changes and deformation.
⑤ There are undercuts in mold, causing deformation when mold is released. The way to improve it is to reduce depth of undercuts and increase corner R wherever possible and save mold slip.
⑥ If ejector pins are too small, number is too small or distribution is unreasonable, these will make ejection unbalanced and need to be improved accordingly.
⑦ Improve exhaust and reduce stress imbalance within plastic parts.
⑧ Add reinforcing ribs at possible locations in mold.
⑨ Adjust mold temperature, use strong water cooling for thick-walled positions, increase temperature for remote thin-walled positions to make the entire piece shrink evenly and reduce internal stress.
(2) Injection molding process
① Increase cooling time.
② Adjust injection pressure to reduce screw forward time.
③ Reduce screw speed and back pressure to reduce material density while ensuring charging.
④ Material temperature is too high or too low, adjust according to specific situation.
⑤ Eject plastic part slowly.
⑥ After mold is released, use fixture to shape it and quickly cool it in water.
5. Dimensional instability
Dimensional instability means that size of injection molded part changes beyond allowable range. Dimensional instability may be caused by injection molding machines, molds and processes.
(1) Injection molding machine
① Different types of injection molding machines lead to differences in molding process conditions.
② If melt temperature fluctuates, check whether thermocouple and temperature controller are faulty.
③ Screw speed and stopping action are unstable, check hydraulic system.
④ Unstable injection pressure, check whether there is constant melt buffering in each cycle, whether return plastic flow valve is leaking, etc., and repair or replace it accordingly.
(2) Mold
① Check whether there is any residue blocking the gate.
② Whether mold temperature is constant, whether coolant channel is smooth, and whether cooling circuit is correctly connected.
③ Check whether there is any problem with mold forming components.
(3) Injection molding process
① If mold temperature control is unreasonable due to uneven mold temperature or improper cooling circuit, make corresponding adjustments.
② Injection pressure is low, increase injection pressure.
③ Appropriately increase injection time and pressure holding time.
④ Barrel temperature or nozzle temperature is too high, adjust accordingly.
⑤ Model filling is too slow, increase injection speed or use multi-stage filling speed.
2 thoughts on “Solutions to mold opening problems for plastic products (3)”